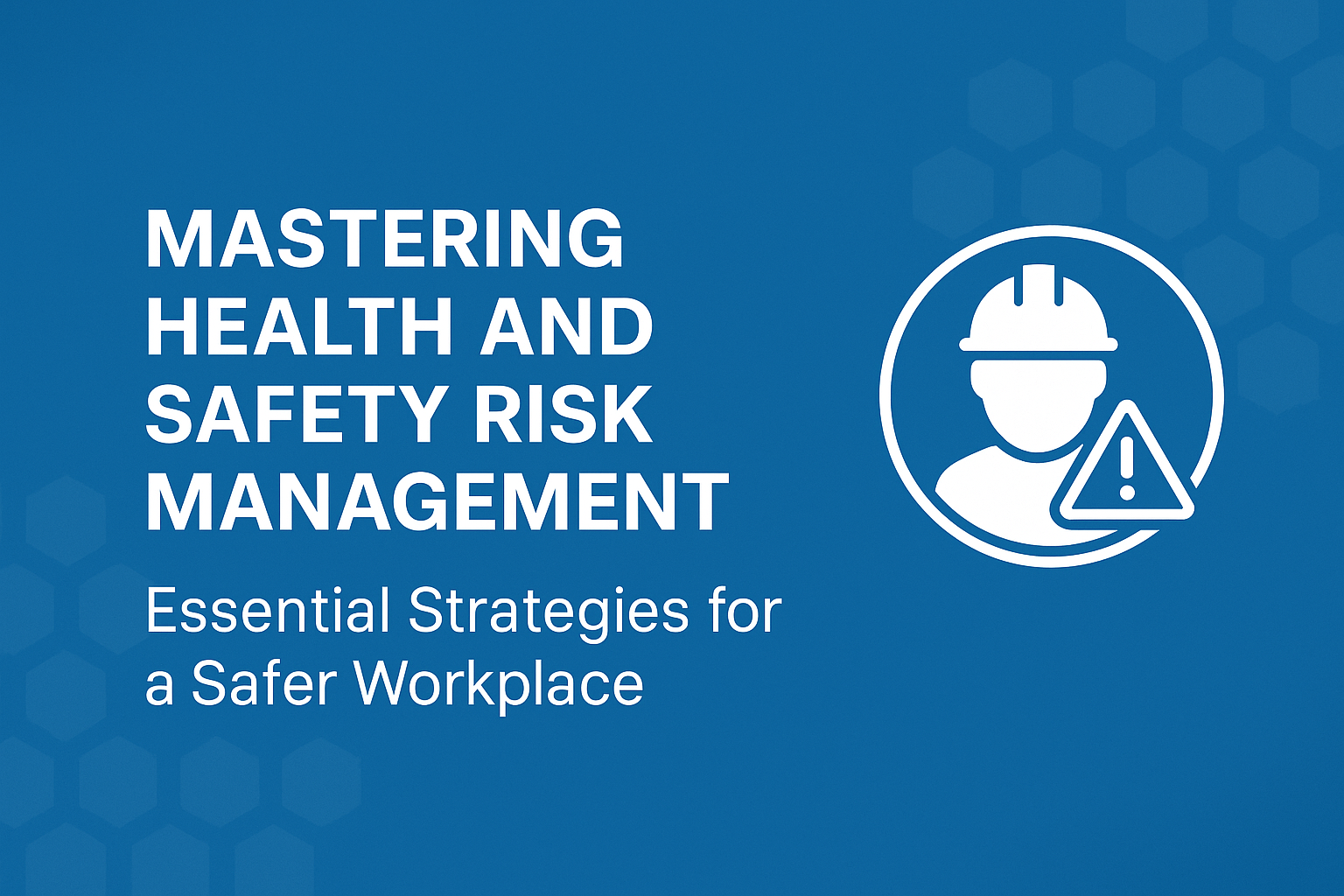
Introduction
In today’s fast-paced and dynamic work environments, health and safety are more important than ever. A safe workplace is not only a legal obligation but also a moral responsibility and strategic advantage. Organizations that prioritize health and safety tend to experience higher employee morale, increased productivity, and lower operational costs. However, many businesses struggle to adopt a proactive and structured approach to identifying and mitigating workplace risks. Mastering health and safety risk management requires a deep understanding of essential strategies tailored to an organization’s unique operational landscape. This article explores the core elements of effective risk management, offering practical strategies that can be implemented to create a safer and more resilient workplace.
Understanding Health and Safety Risk Management
Health and safety risk management involves the systematic process of identifying, assessing, and controlling hazards in the workplace to prevent accidents, injuries, and illnesses. This discipline ensures that risks are managed in a way that protects employees, maintains business continuity, complies with legal regulations, and promotes an overall culture of safety.
Effective risk management starts with identifying different types of hazards, including physical (e.g., slips, trips, and falls), chemical (e.g., exposure to harmful substances), biological (e.g., viruses, bacteria), ergonomic (e.g., poor workstation design), and psychosocial (e.g., stress, harassment). Each of these hazards requires targeted strategies and ongoing monitoring. Importantly, health and safety risk management is not a one-time task but a continuous cycle of improvement and vigilance.
The Importance of Risk Management in the Workplace
Prioritizing risk management is vital for safeguarding employee well-being and enhancing organizational performance. A well-managed health and safety program reduces workplace incidents, minimizes downtime, and builds employee trust. When employees feel safe, they are more engaged, loyal, and productive.
Financially, effective risk management reduces costs associated with workplace injuries, such as medical expenses, legal fees, compensation claims, and insurance premiums. It also helps avoid operational disruptions and reputational damage resulting from safety incidents.
Moreover, organizations must comply with a range of occupational health and safety regulations. Regulatory bodies impose strict standards and penalties for non-compliance. Companies that maintain compliance not only avoid penalties but also demonstrate a commitment to ethical and responsible business practices.
Key Components of a Successful Risk Management Plan
A successful health and safety risk management plan includes several critical components:
- Leadership Commitment: Senior management must champion safety initiatives, allocate necessary resources, and establish clear safety policies. Leadership commitment sets the tone for a strong safety culture throughout the organization.
- Hazard Identification and Risk Assessment: Regular workplace inspections, audits, and analyses help identify potential hazards. Risk assessments evaluate the likelihood and severity of these hazards, helping prioritize control measures.
- Implementation of Control Measures: Controls are classified into engineering controls (e.g., machine guards), administrative controls (e.g., training, procedures), and personal protective equipment (PPE). These measures aim to eliminate or reduce risks effectively.
- Monitoring and Evaluation: Ongoing monitoring ensures that control measures are functioning as intended. Performance metrics, audits, and incident reports help track safety outcomes and identify areas for improvement.
- Employee Involvement and Communication: Involving employees in safety programs encourages accountability and shared responsibility. Open communication channels enable reporting of hazards, feedback, and continuous learning.
Identifying Workplace Hazards: Methods and Tools
Identifying hazards is the foundation of any risk management process. Various tools and methods can assist in this process:
- Walk-through Inspections: Safety officers or supervisors conduct regular inspections to identify visible hazards in the workplace.
- Job Safety Analysis (JSA): Each job is broken down into individual tasks, and risks associated with each task are identified.
- Hazard Identification Checklists: Structured forms that help assess risks associated with specific activities or environments.
- Employee Feedback and Observation: Employees are often the first to notice emerging risks and can provide valuable insights.
Risk Assessment Techniques: Qualitative and Quantitative Approaches
- Qualitative: Uses descriptive scales like low, medium, or high to assess risks. These are easy to apply and useful for routine evaluations but may lack precision.
- Quantitative: Involves numerical analysis using statistical models and data. Techniques like fault tree analysis or event tree analysis offer more accuracy but require more resources.
A combination of both approaches provides a balanced view, allowing organizations to prioritize high-risk areas while managing routine hazards effectively.
Developing Effective Control Measures
Control measures are implemented to mitigate or eliminate identified risks:
- Engineering Controls: Modify the physical environment or equipment to remove hazards (e.g., installing exhaust ventilation, ergonomic tools).
- Administrative Controls: Include safety policies, shift rotations, procedures, and employee training to guide safe practices.
- Personal Protective Equipment (PPE): Equipment such as gloves, goggles, and helmets serve as the last line of defense against exposure.
Controls should be selected based on the hierarchy of hazard control—starting with elimination and substitution before relying on PPE.
Training and Communication: Engaging Employees in Safety
An effective safety program hinges on well-informed and engaged employees. Training ensures that employees understand risks, use equipment properly, and follow procedures. Key components include:
- Onboarding Training: Introduces new employees to safety policies and procedures.
- Refresher Courses: Reinforces knowledge and updates on new safety practices.
- Emergency Drills: Prepare staff for potential crises.
Clear communication ensures that safety messages reach all levels of the organization. Regular safety meetings, posters, digital notices, and toolbox talks keep employees informed and involved.
Monitoring and Reviewing Risk Management Practices
Continuous improvement is central to risk management. Regular monitoring helps track the effectiveness of controls and identify new risks:
- Safety Audits and Inspections: Evaluate compliance with policies and identify improvement areas.
- Incident Reporting and Investigation: All incidents, including near-misses, must be reported and analyzed to uncover root causes.
- Performance Metrics: Tracking metrics such as incident rates, training completion, and hazard reports helps assess safety performance over time.
Corrective actions based on review findings should be implemented promptly, and lessons learned should be integrated into future risk management plans.
Legal Compliance and Industry Standards
Organizations must stay updated with local and international health and safety regulations. This includes:
- Legal Requirements: Such as national labor laws and occupational safety regulations (e.g., OSHA, Factories Act, GOSI).
- Industry Standards: Voluntary frameworks like ISO 45001 that provide structured guidance for safety management systems.
Non-compliance can result in financial penalties and reputational damage. By aligning with legal and best-practice standards, companies demonstrate due diligence and commitment to employee welfare.
Conclusion: Building a Culture of Safety
Mastering health and safety risk management is not just about compliance—it’s about creating a workplace where safety is woven into the organizational culture. By integrating leadership commitment, proactive hazard identification, risk assessments, effective controls, and continuous employee engagement, organizations can significantly reduce workplace incidents and foster a resilient and productive environment.
A strong safety culture empowers employees at all levels to take responsibility for their well-being and that of their colleagues. This collaborative approach leads to long-term success, not only in safety metrics but also in overall organizational performance.